Online Technical Training Blog
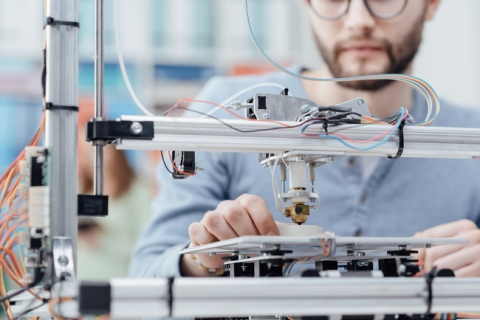
How 3D Printing Electronic Components Is Changing the Face of Manufacturing
Undoubtedly, the rise of new technologies, namely within the virtual reality (VT), augmented reality (AR) and augmented intelligence (AI) realms have changed the way consumers and businesses perceive the world around them, the world in which they work, and the products they consume and manufacture. Operating within this innovative realm is the rise of 3D printing, whose maturity has reached the point where complex electronic components can now be constructed entirely through computer-aided design (CAD) models and realized through highly-specialized 3D printers.
In order to best understand how far-reaching this technology is, it’s important to understand the current state of the 3D printing realm, companies currently pioneering this field, and its current applications and opportunities for improvement.
An Overview of 3D Printing of Electronic Components
There are several ways a manufacturer, or printer, can go about 3D printing electronic components. However, the most popular method remains implementing a dual-material fused filament process that makes use of thermoplastic filaments. The filaments in questions are typically made from copper, but increasingly, carbon and graphene are also used. Once the material has been chosen, the process from design to realization of the component is surprisingly straightforward.
First, a digital CAD model of the component needs to be designed. This design will serve as the blueprint for the printer, as it will provide the printer all the required disional data to build (read: print) the component.
Once the printing process has begun, a “trace” is created. A trace is akin to a fingerprint, with various instructional lines for the printer. From here, the requisite materials are added upon the trace in layers, building up the structure of the component.
A key challenge of 3D printing electronic components compared to other objects is the need to use thicker traces. More robust traces are required to compensate for the fact that conductive ink, paint, or filament that’s used to create the traces has a higher resistance than materials, like copper, that are more commonly used.
Innovative Companies Pioneering the 3D Printing of Electronic Components
Despite the inherent challenges of 3D printing electronic components, there are many companies currently pioneering this space. These companies have made significant forays into this field by manufacturing complex components, which allows them to produce systems that are increasingly scalable and efficient. Some of the companies in question include:
Nano Dimension
Nano Dimension’s flagship platform is its DragonFly Lights-Out Digital Manufacturing (LDM) system for electronic circuitry. As its name suggests, this system doesn’t require any human assistance and can be left to run even with the lights off as employees leave for the day. DragonFly LDM integrates a precise inkjet deposition printer with dedicated nano-inks and 3D software to print electronic circuits, including printed circuit boards (PCBs), antennas, capacitors and sensors.
Optomec
Optomec is currently focusing their efforts on Aerosol Jet technology and has developed a 3D printer capable of printing interconnects, traces, and even passive and active components on 2D and 3D substrates. The printers that make use of this Aerosol Jet 3D printing system are able to print on a multitude of substrates, including plastics, ceramics and metallic structures. Additionally, Aerosol Jet printers can print conformal interconnects on 3D surfaces, eliminating the need for wire bonding.
Current Applications & Areas for Improvement
As is expected, there is a host of benefits associated with 3D printing in general, and specifically for the printing of electronic components. Chief among these advantages include: mass customization, greater design freedom, tooling reductions and packing efficiencies. Looking to the future, companies like Optomec hope to add biological component printing to their list of printer capabilities. Additionally, as the need to operate within smaller spaces remains a key driving factor of innovation, Optomec is also looking to more tightly integrate electronic circuitry with physical packaging to fuel growth within new consumer and military applications.
While these advances are undoubtedly laudable, there are still many hurdles that the 3D printing industry must overcome, especially in the printing of complex components (like PCBs), in order to become available on a larger scale. Currently, the energy consumption of 3D printers printing electronic components is much higher than that of traditional manufacturing systems, and the printing process itself is still quite slow. Furthermore, as more consumers and companies gain access to sophisticated 3D printers, the less complex the design and printing process becomes, the more difficult it will be to stop the illegal manufacturing or “pirating” of proprietary technology.
Undoubtedly, 3D printing will continue to permeate throughout the manufacturing vertical and develop commercial uses. While many advances have already been made, manufacturers have yet to unlock the full potential of 3D printing. Arguably, the next logical step within the 3D printing realm is automation. By automating the 3D printing process, companies will be able to help rapid prototypers cut costs, and add value to stakeholders. This will surely open more doors for those interested in pursuing automation training online and pursuing a career as an automation or robotics technician.
Between changing the face of collaborative design and manufacturing process, shrinking lead times, and creating previously impossible to manufacture products, 3D printing and a new generation of manufacturing and design engineers will transform not just design but the very objects we use in our business and personal lives.